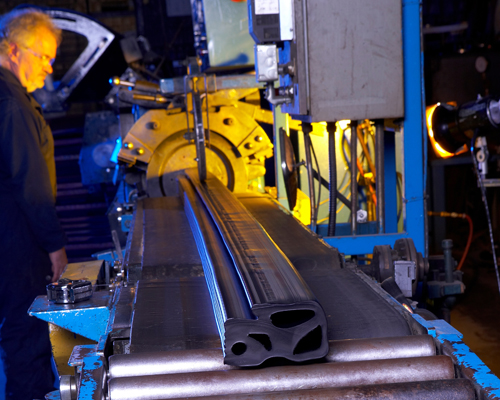
It was in 1988 that BF Goodrich, the company that first discovered how to bond rubber to steel, decided to divest the industrial businesses it had accrued and focus on its aerospace assets. The US rubber lining business was sold to RJF International Corporation, while its Canadian operations to Epton Industries Incorporated. In 1996, Peter Snucins purchased the assets and intellectual property of Epton Industries and created Polycorp Ltd in Elora, Ontario. On August 26, 2002 Polycorp purchased Polymeric Protective Linings, the RJF International business, establishing Polycorp as the largest manufacturer of rubber linings in North America, and heir to an accumulation of unrivalled know-how in the field of polymers going back nearly 90 years.
There are many industrial applications for rubber. Polycorp made an early decision to focus its R&D investment and marketing on just three strategic areas: Transportation, Protective Linings and Mining. “One of the things that makes our company unique is that we have these three divisions,” says Vice-President and General Manager Andrew Haber. What is common to each division is the design and use of rubber to protect against corrosion, wear, impact, noise and vibration.
The three divisions, all serving growing markets, are roughly the same size when it comes to sales turnover. The key strategy in each sector is to position Polycorp strongly with its customers in North America, then expand into markets around the world where similar technologies and issues are encountered. The policy has been a success as evidenced by its sales growth – from $66 million in 2012 to an expected $75 million this year. “The target is to hit $100 million by 2015,” says Haber, “and this will be largely achieved through export growth.”
Transportation does not adequately describe what the first of these divisions does, though it was this market that prompted Polycorp's owner, President and CEO Peter Snucins to purchase the company in the first place. Polycorp’s Epflex Railseal Interface is designed to match the contours of the rail at freight railroad level grade crossings. Epflex Railseal Interface is an extruded virgin rubber profile designed to absorb the destructive energy from both rail deflection and vehicular traffic thereby extending the crossing life and significantly cutting maintenance costs. “Polycorp guarantees Epflex Railseal Interface to be reusable for at least two grade crossing rehabilitations. This translates to a lower cost per year in crossing maintenance when amortized over the products life,” Haber says.
In recent years, the Transportation division has developed a Track Encapsulation System for urban transit systems. “We looked at the expanding market in light rail transit systems, street cars and tramways being installed across North America in cities such as Toronto Ontario, Salt Lake City Utah and Houston Texas,” says Haber. A rubber system provides several benefits in these applications. Noise and vibration reduction is very important in urban areas of course, but these systems also call for the electrical isolation of the whole rail, since what is called 'stray current corrosion' can damage pipes and other underground structures in the vicinity. With many North American cities installing or extending transit networks, this is a growing market segment for Polycorp. These projects do not happen overnight and there is always a long commissioning and engineering design stage to go through. To develop the international market, Polycorp is working with engineering design firms such as Alstom, transferring North American designs and technology to other geographic regions.
The Protective Linings division is where Polycorp’s chemistry expertise comes in strongest. It has a huge portfolio of over 80 lining formulations and decades of proven performance in their application in industrial situations that call for protection of tanks, pipes and equipment from corrosive or abrasive environments. The material is supplied uncured, applied and then cured in situ to form a continuous protective rubber membrane. In many cases the lining can last over ten years, dramatically increasing asset life for customers. “An engineer can expect to specify these materials only a couple of times in their career. Mitigating the risk associated with hazardous materials is a key factor in their decision making process,” Haber says. Polycorp chemists are constantly working with customers to develop new formulations to suit whatever aggressive chemicals they may need to handle.
Mining, the third division, is particularly buoyant at this time. In this market, Polycorp is a leader in designing and manufacturing grinding mill liners. Ball mills, semi-autonomous grinding and autonomous grinding mills require a replaceable liner systems to protect the mill shell and to enhance the movement of the ore slurry for optimum throughput and grinding performance. Mill liner replacement is a critical part of the entire mining operation. If the mill stops, the whole process stops. It is critical that the mill liners achieve the required service life. “Preventive maintenance schedules depend on replacement on a regular basis. If you are off by a week they have to do an unplanned shutdown – and this can have huge financial consequences,” Haber points out. Mill liners can be designed to last anywhere between three months for aggressive applications in large SAG mills, to a couple of years in smaller ball mills.
There are three types of mill liners, Haber explains, all steel, all rubber and rubber/steel combinations where the rubber is moulded to a steel insert providing protection at the leading edge. Manufacture of these parts is highly customised, with each mill having its own specification and design. Over the last four years Polycorp has focused its R&D toward the advanced design and engineering of these parts, working with Dr R Rajamani at the University of Utah who has developed computer models that simulate the flow of ore slurry through grinding mills. This virtual prototyping approach allows for evaluating different ways mill managers and engineers can run the mill and find what design gives the best efficiency and the longest life to different parts. “Our approach to mining has become more design intensive as opposed to a materials approach. The right formula is one essential ingredient. Mill liner design is just as important in getting performance right.”
Mining looks to represent the largest market potential for Polycorp, with geographic expansion opportunities leading the way. “We are targeting regions under serviced by our competitors. Currently we are pursuing opportunities in Kazakhstan, Mongolia and in emerging resource-driven African countries like Ghana, Mali and Ivory Coast,” says Haber. In these markets, developing local agents with a good understanding of the mine operations is a key.
Manufacturing, engineering, customer service, sales & marketing and product development for each of the divisions is located at the Elora Ontario plant, a lean operation employing just over 150 multi-skilled people. The company has been investing to grow its manufacturing capacity. In 2012 a third calender line for manufacturing Protective Lining products was launched. Currently a very large multi-daylight press and automated handling systems for manufacturing mining products is in the process of being installed. These investments will ensure that Polycorp has the capability to support its $100 million vision.
Last year, the management team was honoured with being raised to the pantheon of Canada’s 50 Best Managed Companies sponsored by Deloitte, CIBC, National Post and Ontario’s Queens School of Business. Re-election as one of Canada’s Best Managed Companies this year, underlines the through-and through excellence of the business. “It provides our customers with independent validation of the soundness of our business strategy and commitment to the industries we serve” says Andrew Haber.
Written by John O’Hanlon, research by Jeff Abbott
DOWNLOAD
Polycorp-AM.Mining-Apr13-Bro-s.pdf